Best Torque Wrench for DIY Mechanics? Dude, that’s a seriously important question! Knowing how to properly tighten bolts isn’t just about making sure things stay put—it’s about preventing serious damage to your car or project. We’re talking stripped threads, broken parts, and even safety hazards. This guide dives deep into choosing the right torque wrench for your DIY needs, covering everything from types and features to safety and maintenance.
Get ready to level up your wrench game!
We’ll break down the different kinds of torque wrenches – clicker, beam, and digital – and help you figure out which one best fits your budget and the types of projects you tackle. We’ll also cover crucial features like accuracy, torque range, and drive size, plus offer tips on proper usage and maintenance to keep your wrench calibrated and ready to go.
Think of this as your ultimate guide to becoming a torque-wielding DIY master.
Introduction to Torque Wrenches for DIY Mechanics
So, you’re diving into the world of DIY auto repair – awesome! But before you start wrenching, let’s talk about a crucial tool that’ll save you headaches (and potentially expensive repairs): the torque wrench. Think of it as your secret weapon against stripped bolts, broken parts, and a whole lot of frustration. Using a torque wrench correctly is key to ensuring your repairs are both effective and safe.Using a torque wrench is essential for any DIY mechanic tackling automotive repairs.
Over-tightening or under-tightening bolts can lead to serious problems, ranging from minor leaks and stripped threads to catastrophic component failure. This can mean the difference between a simple fix and a much more costly repair, or even a dangerous situation while driving. It’s all about precision and getting the job done right the first time.
Picking the best torque wrench for DIY mechanics is crucial for safe and reliable repairs. You’ll need it for things like changing your brakes or, if you’re experiencing a grinding noise while driving, maybe you should check out this article on Symptoms of a bad wheel bearing before you start wrenching, as a bad bearing could impact other components.
Getting the right torque is key to preventing damage, so investing in a good quality wrench is a smart move for any DIYer.
The Risks of Improper Bolt Tightening
Over-tightening bolts can easily strip the threads, rendering the bolt useless and requiring costly replacement of the entire bolt and potentially the part it secures. This can lead to leaks (oil, coolant, etc.), loss of functionality, and even safety hazards. For instance, over-tightening a lug nut could lead to a wheel coming loose while driving. On the other hand, under-tightening bolts results in loose connections, which can cause vibrations, leaks, and eventual component failure.
Imagine a loose exhaust manifold bolt leading to a rattling exhaust and potential damage to the catalytic converter. These are not situations you want to find yourself in.
A Brief History of Torque Wrenches, Best torque wrench for DIY mechanics
The concept of controlled tightening has been around for a while, but the first truly practical torque wrenches emerged in the early 20th century. Early models were often quite cumbersome and relied on mechanical mechanisms to indicate the applied torque. These early designs were primarily used in industrial settings. As technology advanced, more sophisticated designs emerged, including beam-type wrenches, click-type wrenches, and finally, digital torque wrenches that offer precise readings and often include features like preset torque settings and data logging.
This evolution has made torque wrenches more accessible and user-friendly for DIY mechanics.
Types of Torque Wrenches
Choosing the right torque wrench can make all the difference in your DIY projects. Getting the torque right is crucial for preventing stripped bolts, damaged parts, and ultimately, a botched repair. But with several types available, knowing which one suits your needs and budget is key. This section breaks down the three main types: clicker, beam, and digital.
Clicker Torque Wrenches
Clicker wrenches are probably the most common type you’ll encounter. They operate by using a calibrated mechanism that produces an audible “click” when the pre-set torque is reached. This provides tactile and auditory feedback, letting you know exactly when to stop applying force.Advantages for DIY use include their relatively low cost and ease of use. They’re straightforward to set and use, making them ideal for occasional DIYers.
They’re also generally durable and require minimal maintenance.Disadvantages include the potential for slight inaccuracy, particularly with repeated use. The “click” itself might be subtle or difficult to hear in noisy environments. Also, the setting mechanism can sometimes be fiddly, requiring careful adjustment.
Beam Torque Wrenches
Beam torque wrenches utilize a simple yet effective design. A calibrated beam deflects visibly when the pre-set torque is reached. A pointer on the beam indicates whether the torque has been achieved. These wrenches are often favored for their simplicity and robustness.Their primary advantage lies in their mechanical simplicity and resulting durability. They’re generally less prone to damage than electronic counterparts and are often quite affordable.
The visual indication is clear and easy to understand, even in less-than-ideal conditions.The disadvantages are that the accuracy can be somewhat limited, especially at the lower and higher ends of the torque range. The visual reading can also be subjective, depending on lighting and the user’s ability to precisely interpret the deflection of the beam.
Digital Torque Wrenches
Digital torque wrenches are the high-tech option. They use an electronic sensor to measure torque and display the reading on a digital screen. These wrenches offer precision, often with features like peak torque readings, various units of measurement (Nm, ft-lb, in-lb), and sometimes even data logging capabilities.For DIYers, the advantages are clear: high accuracy and ease of reading. The digital display eliminates any guesswork or subjective interpretation.
Many models also offer multiple torque units and memory functions, adding convenience.However, digital torque wrenches are usually the most expensive option. They also require batteries, which can run out at inconvenient times. Finally, they’re more susceptible to damage than their mechanical counterparts, especially if dropped or mishandled.
Comparison Table
Feature | Clicker | Beam | Digital |
---|---|---|---|
Accuracy | Moderate | Moderate | High |
Ease of Use | High | High | High |
Cost | Low | Low to Moderate | High |
Durability | Good | Excellent | Moderate |
Suitability for DIY | Excellent for occasional use | Good for occasional to regular use | Excellent for precise work, but costlier |
Features to Consider When Choosing a Torque Wrench
Picking the right torque wrench for your DIY projects can feel overwhelming, but focusing on key features simplifies the process. The right tool ensures you avoid over-tightening (damaging bolts and threads) or under-tightening (leading to loose parts and potential safety hazards). Consider these essential features to make an informed decision.
Accuracy and Calibration
Accuracy is paramount when working with torque wrenches. A wrench that’s consistently off by even a small amount can lead to significant problems. For example, an inaccurate wrench could cause a wheel lug nut to loosen prematurely, leading to a dangerous situation. Calibration refers to the process of verifying a wrench’s accuracy against a known standard. Regular calibration, ideally annually or after heavy use, is crucial for maintaining accuracy.
Many higher-end torque wrenches offer calibration certifications, ensuring they meet specific accuracy standards. Look for wrenches with stated accuracy tolerances, usually expressed as a percentage of the applied torque. Lower tolerances indicate greater precision.
Torque Range and Drive Size
The torque range specifies the minimum and maximum torque values the wrench can accurately measure and apply. Choose a range that covers the majority of your DIY projects. A wrench with too narrow a range might be insufficient for larger jobs, while one with an excessively wide range might be less precise at the lower end. Drive size refers to the square-drive size (e.g., 1/4 inch, 3/8 inch, 1/2 inch) that accepts sockets.
The drive size you need depends on the size of the fasteners you’ll be working with. Smaller drive sizes are suitable for smaller fasteners, while larger drive sizes are necessary for larger, higher-torque applications. For example, a 1/4″ drive is suitable for smaller fasteners like those found on electronics, while a 1/2″ drive is better suited for larger fasteners like lug nuts.
Additional Features
Several additional features can enhance usability and convenience. A built-in LED light can significantly improve visibility in dimly lit areas, like under a car or in a cluttered workshop. This is especially helpful for working on tight spaces where a flashlight might be cumbersome. Digital displays offer precise torque readings, allowing for better control and accuracy. Some digital torque wrenches even feature preset torque settings, making it easy to switch between different tightening requirements.
Other features, such as audible alerts when the target torque is reached or a click-type mechanism that signals the precise torque setting, improve the user experience and efficiency.
So, you’re building your DIY mechanic toolkit, huh? Picking the best torque wrench is crucial – you don’t want to overtighten anything, especially if you’re working on something as insane as a Hennessey Venom F5; check out the latest on its 2025 road legal status here: Hennessey Venom F5 road legal status 2025. Anyway, back to wrenches – a good quality click-type is a solid investment for any serious DIYer.
Essential Features Checklist for DIY Mechanics
Before purchasing a torque wrench, consider the following checklist:
- Accuracy: Look for a wrench with a stated accuracy tolerance of ±3% or better.
- Torque Range: Select a range that suits the typical fasteners you’ll be working with. Consider the largest and smallest bolts you’ll encounter.
- Drive Size: Choose a drive size appropriate for your projects (e.g., 1/4 inch for small fasteners, 3/8 inch for medium, 1/2 inch for larger ones).
- Calibration: Check if the wrench is easily recalibrated or if calibration services are readily available.
- Ease of Use: Consider the wrench’s ergonomics and how comfortable it is to hold and use for extended periods.
- Durability: Choose a wrench made from high-quality materials that can withstand regular use.
Torque Wrench Usage and Maintenance
Proper torque wrench usage and maintenance are crucial for ensuring accurate tightening and preventing damage to your project. A little care goes a long way in extending the life of your tool and preventing costly mistakes. This section will cover the proper steps for using a torque wrench, best practices for maintenance and calibration, and common errors to avoid.
Using a Torque Wrench
Using a torque wrench correctly is essential to avoid over-tightening or under-tightening fasteners. Incorrect torque can lead to stripped threads, broken parts, or even injury. Follow these steps for accurate and safe usage:
- Select the Correct Socket: Ensure the socket size matches the fastener you’re working on. A loose or ill-fitting socket can cause inaccurate readings and damage the wrench.
- Set the Desired Torque: Adjust the torque wrench to the specified torque value found in your vehicle’s repair manual or the manufacturer’s instructions. This value is typically expressed in either pound-feet (lb-ft) or Newton-meters (Nm).
- Attach the Socket: Securely attach the selected socket to the wrench’s square drive.
- Position the Wrench: Position the wrench on the fastener, ensuring a straight line of force is applied. Avoid applying any sideways pressure.
- Apply Torque Slowly and Steadily: Slowly and steadily apply force to the wrench until you hear or feel the click indicating the desired torque has been reached. Do not jerk or rapidly twist the wrench.
- Remove the Wrench: Once the click is heard or felt, immediately release the pressure and remove the wrench from the fastener.
Torque Wrench Maintenance and Calibration
Regular maintenance is key to ensuring your torque wrench remains accurate and reliable. Neglecting maintenance can lead to inaccurate readings and potentially damage your project.
- Regular Cleaning: Keep your torque wrench clean and free of debris. Use a soft cloth and mild solvent to clean the wrench after each use.
- Proper Storage: Store your torque wrench in a clean, dry place away from extreme temperatures and direct sunlight. Always return the wrench to its lowest torque setting after use.
- Periodic Calibration: Torque wrenches should be calibrated regularly, ideally annually or more frequently depending on usage. Professional calibration ensures accuracy and helps prevent costly mistakes. Many tool rental shops offer this service.
Torque Unit Conversion
Often, torque values are provided in different units. Knowing how to convert between units is important for accurate work. The most common conversion is between lb-ft and Nm. The conversion factor is:
1 lb-ft = 1.356 Nm
For example, to convert 50 lb-ft to Nm:
50 lb-ft
1.356 Nm/lb-ft = 67.8 Nm
Common Mistakes to Avoid
Avoiding these common mistakes will ensure you get accurate and safe results every time you use your torque wrench.
- Ignoring the Click: Continuing to apply force after the click can damage the wrench and over-tighten the fastener.
- Using the Wrong Socket: A loose or incorrect socket size leads to inaccurate readings and can damage the fastener or wrench.
- Applying Angled Force: Applying force at an angle instead of directly along the wrench’s axis leads to inaccurate readings.
- Neglecting Maintenance and Calibration: Regular cleaning, proper storage, and periodic calibration are essential for maintaining accuracy.
- Using a Damaged Wrench: A damaged torque wrench will provide inaccurate readings and should be repaired or replaced.
Budget-Friendly Options vs. Professional-Grade Torque Wrenches: Best Torque Wrench For DIY Mechanics
Choosing the right torque wrench can feel overwhelming, especially with the wide range of prices and features available. The difference between a budget-friendly option and a professional-grade wrench often comes down to build quality, accuracy, and long-term durability. Understanding these differences will help you make an informed decision based on your DIY needs and budget. This section explores the trade-offs between cost and quality, highlighting examples to guide your purchase.Budget-friendly torque wrenches often sacrifice some features and precision for a lower price point.
While perfectly suitable for occasional DIY projects, they may lack the accuracy and longevity of their professional counterparts. Professional-grade wrenches, conversely, boast higher accuracy, sturdier construction, and often include additional features like calibration certificates and longer warranties. The increased cost reflects the superior materials, more rigorous manufacturing processes, and enhanced performance.
Key Differences Between Low-Cost and High-End Torque Wrenches
The differences between low-cost and high-end torque wrenches are significant and directly impact accuracy, reliability, and lifespan. Consider these key factors before making a purchase.
- Accuracy: Professional-grade wrenches typically offer significantly higher accuracy, often within ±2% or even ±1% of the set torque value. Budget options might have a wider margin of error, potentially leading to over-tightening or under-tightening of fasteners.
- Durability: High-end torque wrenches are usually made from higher-quality materials, such as chrome vanadium steel, resulting in greater resistance to wear and tear. Budget models might use less durable materials, making them more prone to damage with extended use.
- Calibration: Professional wrenches often come with a calibration certificate, verifying their accuracy. Budget wrenches usually lack this feature, requiring periodic professional calibration at additional cost.
- Features: Professional wrenches may include features like dual-scale displays, quick-release mechanisms, and more robust handles. Budget options generally have fewer features and simpler designs.
- Warranty: High-end brands typically offer longer warranties, reflecting their confidence in the product’s durability. Budget wrenches usually come with shorter warranties or no warranty at all.
Examples of Good Value Torque Wrenches
Finding a balance between price and performance is key. Here are some examples illustrating this across different price points (note that specific models and pricing change frequently, so always check current reviews and prices before purchasing):
- Budget-Friendly (<$50): Many brands offer basic click-type torque wrenches in this range. These are adequate for infrequent use on smaller projects, but accuracy and longevity may be limited. Expect a wider margin of error and less robust construction.
- Mid-Range ($50-$150): This price bracket often provides a good balance between features and cost. You can find more accurate click-type wrenches, beam-type wrenches, or even some digital options with improved accuracy and durability compared to the budget options. Look for wrenches with chrome vanadium steel construction.
- Professional-Grade ($150+): At this level, expect top-tier accuracy, robust construction, often with features like calibration certificates and extended warranties. These wrenches are designed for frequent, demanding use and offer the highest precision and reliability.
Torque Wrench Safety Precautions
Using a torque wrench might seem straightforward, but neglecting safety precautions can lead to serious consequences, from damaged components to personal injury. Proper technique and awareness are crucial for safe and effective torque wrench use. This section details essential safety measures to protect yourself and your work.
The most important aspect of torque wrench safety is understanding and adhering to the manufacturer’s instructions. These instructions provide specific guidance on the safe operation, maintenance, and storage of your particular wrench. Ignoring these instructions could void warranties and, more importantly, compromise your safety.
Correct Torque Specifications
Using the correct torque specifications is paramount. Incorrect torque can strip threads, damage fasteners, or weaken critical connections. Always consult your vehicle’s repair manual or a reliable source for the precise torque values for each specific bolt or nut. These specifications are usually expressed in foot-pounds (ft-lb), inch-pounds (in-lb), or Newton-meters (Nm). Using the wrong unit or a miscalculated value can have significant repercussions.
For instance, over-tightening a wheel lug nut could cause it to break, leading to a wheel detaching while driving. Conversely, under-tightening a head bolt on an engine could result in a catastrophic engine failure.
Potential Hazards of Improper Torque Wrench Use
Improper torque wrench use presents several hazards. Over-tightening can cause bolt breakage, stripping of threads, or damage to the connected parts. This could lead to component failure, requiring costly repairs or replacements. Under-tightening, on the other hand, can result in loose connections, leading to leaks, vibrations, or even complete component detachment during operation. For example, under-tightening a bolt on a brake caliper could lead to brake failure, causing a serious accident.
Similarly, improperly torqued engine components can cause oil leaks or misalignment, resulting in significant engine damage.
Safe Storage and Transportation of a Torque Wrench
Proper storage and transportation are crucial for maintaining the accuracy and longevity of your torque wrench. Always store the torque wrench in a clean, dry place, away from extreme temperatures and direct sunlight. Avoid dropping or impacting the wrench, as this can damage the internal mechanism and affect its accuracy. When transporting the torque wrench, use a protective case or padded container to prevent damage during transit.
This will help ensure the wrench remains calibrated and functional for years to come. For example, a sudden drop from a workbench could easily damage the internal components of a click-type torque wrench, affecting its accuracy and potentially leading to inaccurate tightening.
Illustrative Examples of Torque Wrench Applications
So, you’ve got your shiny new torque wrench. Now what? Let’s look at some common DIY automotive scenarios where a torque wrench is absolutely essential to prevent damage and ensure a safe, properly functioning vehicle. Using the wrong torque can lead to stripped threads, broken parts, and even safety hazards, so precision is key.
Changing a Wheel Lug Nut
Changing a tire seems straightforward, but tightening those lug nuts to the manufacturer’s specified torque is crucial for safe driving. Incorrect tightening can lead to wheel wobble, premature wear, or even a wheel detaching while driving. Let’s say you’re working on a 2018 Honda Civic. The recommended torque for the lug nuts is typically between 80-90 ft-lbs (108-122 Nm).
The correct procedure involves tightening the nuts in a star pattern (opposite nuts first) to ensure even pressure distribution. First, hand-tighten each nut, then use the torque wrench to tighten each to the specified range. Failure to use the correct torque can result in loose wheel nuts, leading to potential accidents, or over-tightened nuts, which can strip the threads or warp the wheel.
Installing a New Spark Plug
Spark plugs are another area where precise torque is vital. Over-tightening can crack the porcelain insulator or damage the cylinder head, while under-tightening can lead to a loose spark plug and potential misfires or engine damage. For example, a 2022 Toyota Camry might specify a torque of 15-20 ft-lbs (20-27 Nm) for its spark plugs. The procedure involves carefully inserting the new spark plug, then using the torque wrench to tighten it to the specified range.
A common mistake is using too much force, leading to a cracked spark plug or damaged threads in the cylinder head. This would require expensive repairs to the engine.
Replacing Brake Caliper Bolts
Brake calipers need to be securely fastened to the caliper bracket, but excessive torque can strip the threads or damage the bracket. Conversely, insufficient torque could lead to a loose caliper, resulting in brake failure – a seriously dangerous situation. A typical torque specification for brake caliper bolts might range from 25-35 ft-lbs (34-47 Nm), depending on the vehicle make and model.
The correct procedure involves cleaning the threads and applying a small amount of anti-seize compound before installing the bolts. The torque wrench ensures the bolts are tightened evenly and securely, preventing loosening or damage. Using incorrect torque here can lead to brake problems, from reduced braking power to complete brake failure, which has obvious safety implications.
Epilogue
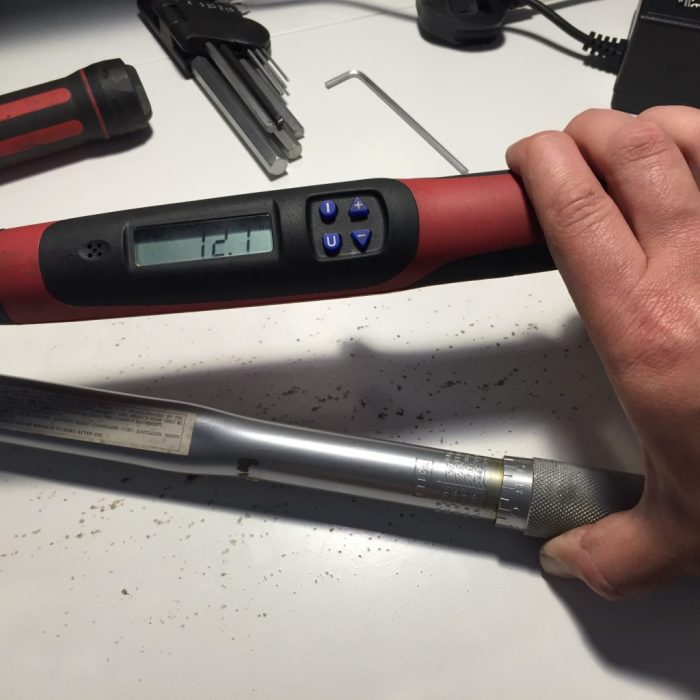
So, there you have it – your comprehensive guide to finding the best torque wrench for your DIY adventures. Remember, choosing the right tool is half the battle. With a little knowledge and the right equipment, you’ll be tightening bolts with confidence, knowing you’re doing it safely and correctly. Now get out there, tighten those nuts, and build something awesome!